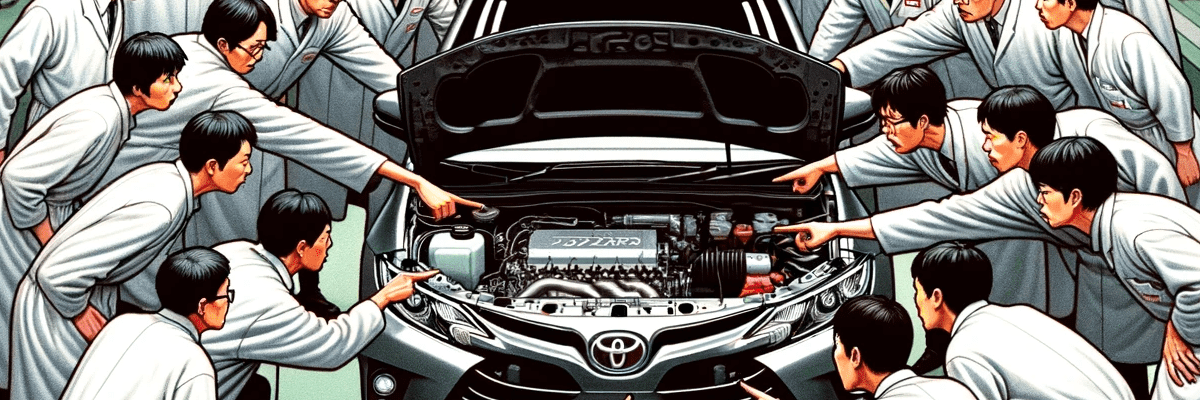
Four great process improvement examples (to learn from)
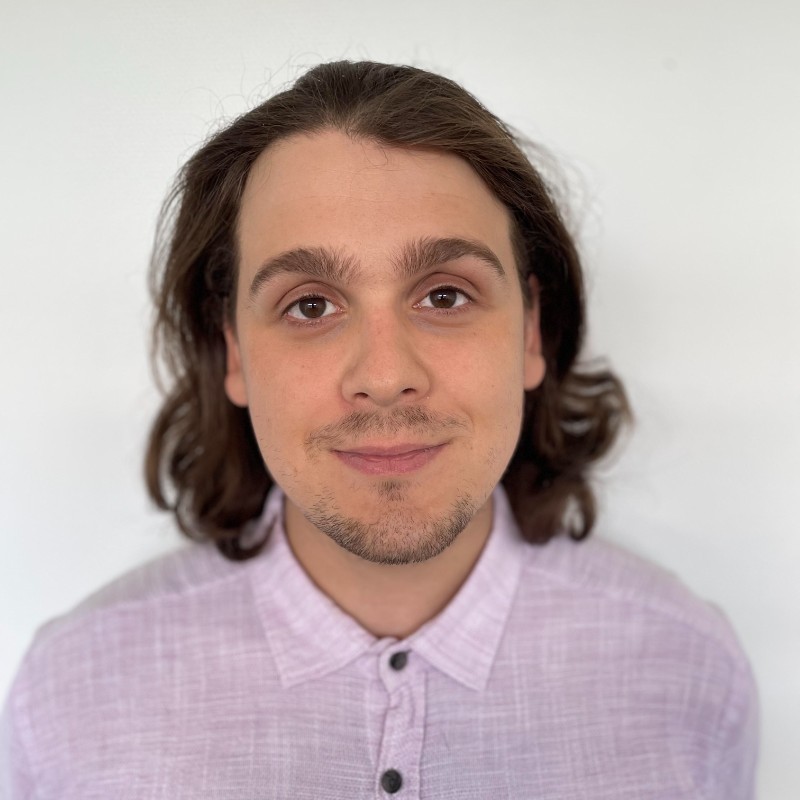
In today’s rapidly changing business landscape, organizations are constantly seeking ways to improve their processes. With the ever-increasing demands of customers and the need to stay competitive, process improvement has become a top priority. In this article, we will explore four great examples of process improvement that organizations can learn from. These examples showcase the power of implementing user-friendly processes, reducing waste to increase efficiency, utilizing process visualization tools, creating standardized processes for scalability, and streamlining business processes with automation. Let’s delve deeper into each of these examples.
Looking for something else? Maybe this article is more relevant:
Implementing User-Friendly Processes
One of the key factors in successful process improvement is ensuring that the processes are user-friendly. When processes are complex and difficult to navigate, employees may struggle to perform their tasks efficiently. By implementing user-friendly processes, organizations can enhance productivity and reduce errors.
For example, a manufacturing company revamped its production line processes to make them more user-friendly. They simplified the steps required to complete each task, provided clear instructions, and trained employees on the new processes. As a result, employees were able to perform their tasks more effectively, leading to increased productivity and reduced errors.
Moreover, the company also focused on creating visual aids to further enhance the user-friendliness of the processes. They developed color-coded charts and diagrams that clearly illustrated the workflow, making it easier for employees to understand and follow. These visual aids not only improved the efficiency of the production line but also reduced the learning curve for new employees.
In addition, the company implemented a feedback system to gather input from employees on the user-friendliness of the processes. They encouraged employees to provide suggestions and ideas for improvement, creating a culture of continuous improvement. This feedback system allowed the company to identify pain points and make further enhancements to the processes, ensuring they remained user-friendly and aligned with employee needs.
Furthermore, the company recognized the importance of providing ongoing training and support to employees to ensure the successful implementation of user-friendly processes. They conducted regular training sessions to familiarize employees with the new processes and address any questions or concerns. Additionally, they assigned process champions who served as mentors and provided guidance to employees, helping them navigate the processes effectively.
Another aspect of user-friendly processes that the company focused on was the use of technology. They leveraged automation and digital tools to streamline and simplify tasks, reducing the reliance on manual processes. This not only improved efficiency but also minimized the chances of errors caused by human intervention.
In conclusion, implementing user-friendly processes is crucial for organizations to enhance productivity and reduce errors. By simplifying steps, providing clear instructions, creating visual aids, gathering employee feedback, offering training and support, and leveraging technology, companies can ensure that their processes are easy to navigate and optimize employee performance.
Examples of features of process improvement
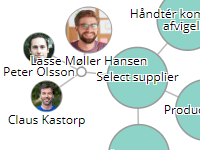
Visual process connection map
Visualize how processes and activities interconnect using filterable, clickable process maps.
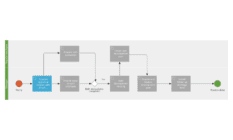
Hold Annual Performance Appraisal
Process outcome: Performance and development review completed and documented.
Increasing Efficiency by Reducing Waste
Another crucial aspect of process improvement is identifying and reducing waste. Waste in processes can take various forms, such as unnecessary steps, excess inventory, or inefficient communication channels. By eliminating waste, organizations can streamline their operations and improve overall efficiency.
A healthcare organization adopted the principles of lean management to identify and reduce waste in their administrative processes. They analyzed their workflows and identified areas of inefficiency, such as redundant paperwork and lengthy approval cycles. By implementing changes like digitizing documents and implementing electronic approval systems, they were able to eliminate waste, resulting in faster processing times and improved employee satisfaction.
One area where the healthcare organization found significant waste was in the handling of patient records. Previously, the administrative staff had to manually retrieve and file physical records, leading to delays and potential errors. By digitizing the records and implementing a centralized electronic system, the organization was able to reduce the time spent on record retrieval and improve accuracy.
In addition to digitizing records, the organization also identified waste in their communication channels. Previously, different departments relied on paper-based memos and emails, leading to delays and miscommunication. By implementing a digital communication platform, they were able to streamline communication, ensuring that information was easily accessible to all relevant parties and reducing the chances of miscommunication.
Another area of waste that the healthcare organization targeted was excess inventory. They found that they were often ordering more supplies than necessary, leading to storage issues and potential waste. By implementing a just-in-time inventory management system, they were able to reduce excess inventory and ensure that supplies were ordered and delivered only when needed.
Furthermore, the organization recognized that employee satisfaction played a crucial role in overall efficiency. They found that lengthy approval cycles and redundant paperwork were causing frustration among the administrative staff. By implementing electronic approval systems and digitizing documents, they were able to simplify processes and reduce the burden on employees, resulting in improved job satisfaction and increased productivity.
Overall, by adopting lean management principles and actively identifying and reducing waste, the healthcare organization was able to significantly improve their efficiency. Through digitization, streamlining communication channels, reducing excess inventory, and prioritizing employee satisfaction, they were able to optimize their administrative processes and achieve better outcomes for both the organization and its patients.
”If you define the problem correctly, you almost have the solution.”
Steve Jobs
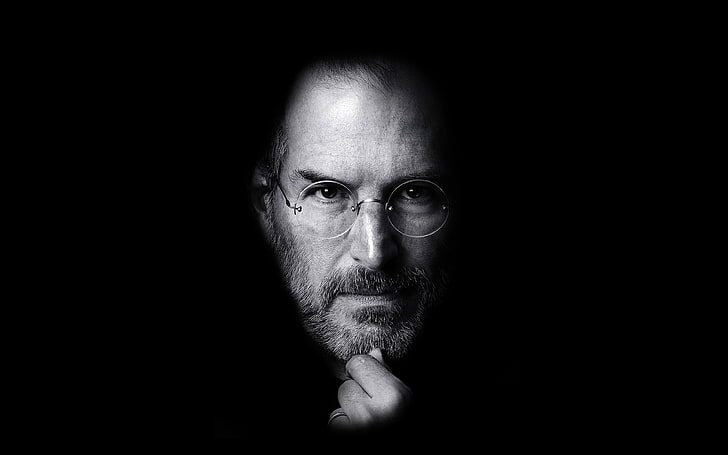
Utilizing Process Visualization Tools
The use of process visualization tools is another effective way to improve processes. Visualization enables employees to better understand complex workflows, identify bottlenecks, and make informed decisions to streamline operations.
A logistics company utilized process visualization tools to enhance their supply chain processes. They mapped out the entire supply chain, from procuring raw materials to delivering the final product. By visualizing the process, they identified areas where delays and bottlenecks occurred and implemented solutions to address them. This led to a smoother supply chain, improved on-time delivery, and increased customer satisfaction.
One of the key benefits of process visualization tools is that they provide a clear and visual representation of the entire workflow. This allows employees to see the bigger picture and understand how each step in the process contributes to the overall outcome. By having this holistic view, employees can identify areas for improvement and make informed decisions to optimize the process.
Moreover, process visualization tools enable employees to identify bottlenecks and areas of inefficiency. These tools provide real-time data and analytics, allowing employees to track the flow of work and identify any areas where work is getting stuck or delayed. By pinpointing these bottlenecks, employees can take proactive measures to address them, such as reallocating resources or redesigning the workflow.
In the case of the logistics company, the process visualization tools helped them identify specific areas in their supply chain where delays were occurring. For example, they discovered that there were delays in the procurement of raw materials, which were causing a ripple effect throughout the entire supply chain. By visualizing this bottleneck, they were able to implement measures to streamline the procurement process, such as establishing better communication channels with suppliers and optimizing inventory management.
Furthermore, process visualization tools also facilitate collaboration and communication among team members. With a visual representation of the workflow, employees can easily share and discuss ideas for improvement. They can identify areas where different teams or departments need to work together to streamline the process and eliminate redundancies. This collaborative approach fosters a culture of continuous improvement and empowers employees to take ownership of the process.
According to tech entrepreneur and investor Draven McConville, “process improvement isn’t just about making things faster — it’s really all about making them better. Get to the heart of your team’s actual workflow challenges, then implement solutions that genuinely address those pain points. Combining standardization with flexibility to adapt to real-world situations works best.”
Overall, process visualization tools are a valuable asset for organizations looking to improve their processes. By providing a visual representation of the workflow, these tools enable employees to better understand the process, identify bottlenecks, and make informed decisions to optimize operations. The logistics company’s success in enhancing their supply chain processes through process visualization serves as a testament to the effectiveness of these tools in driving efficiency and customer satisfaction.
👉 Recommendation: Embrace process visualization tools to map and visualize your business workflows comprehensively. Utilize these tools to identify bottlenecks, inefficiencies, and opportunities for improvement in real time. Encourage collaboration and communication among your teams to streamline processes, enhance efficiency, and ultimately boost customer satisfaction.
Creating Standardized Processes for Scalability
Standardizing processes is crucial for organizations looking to scale their operations. When processes are standardized, it becomes easier to replicate them across multiple locations or departments, ensuring consistency and efficiency.
A retail company expanded its operations to multiple stores and recognized the need for standardized processes. They established a set of standard operating procedures (SOPs) covering various aspects of store operations, such as inventory management and customer service. By following these standardized processes, the company achieved consistency across all stores, enabling smooth operations and better customer experiences.
One of the key benefits of creating standardized processes is the ability to streamline operations. By clearly defining and documenting the steps involved in various tasks, employees can easily follow a set procedure, reducing confusion and minimizing errors. For example, in the case of inventory management, having a standardized process ensures that all stores follow the same guidelines for receiving, storing, and tracking inventory. This not only improves efficiency but also helps prevent stockouts and overstock situations.
Moreover, standardized processes also facilitate training and onboarding of new employees. When there is a clear and well-documented process in place, it becomes easier to train new hires and get them up to speed quickly. The retail company mentioned earlier experienced this firsthand. With their standardized SOPs, they were able to train new store managers and staff efficiently, ensuring that everyone understood the company’s expectations and procedures.
“Standardizing processes is critical when managing teams,” according to Zayed Ahmed, Founder of ASL BPO. “Strong standard operating procedures build trust with clients by showing clear quality controls and delivery standards. They also help maintain high service quality across different shifts and time zones while making it simpler to train new staff members and scale operations based on client needs.”
Another advantage of standardized processes is the ability to identify and address bottlenecks or inefficiencies. When processes are standardized, it becomes easier to analyze and measure their performance. By tracking key metrics and comparing them across different stores or departments, organizations can identify areas that need improvement and implement changes accordingly. This continuous improvement approach helps drive efficiency and scalability.
Furthermore, standardized processes also contribute to better customer experiences. When customers visit different stores or interact with different departments within an organization, they expect a consistent level of service. By having standardized processes in place, organizations can ensure that customers receive the same high-quality service regardless of the location or department they interact with. This consistency builds trust and loyalty among customers, ultimately leading to increased customer satisfaction and retention.
In conclusion, creating standardized processes is essential for organizations looking to scale their operations. It enables consistency, efficiency, and improved customer experiences. By streamlining operations, facilitating training, identifying bottlenecks, and ensuring consistent service, standardized processes lay the foundation for successful scalability.
Streamlining Business Processes with Automation
Automation can greatly contribute to process improvement by reducing manual efforts, minimizing errors, and improving overall efficiency. Organizations can adopt various automation technologies to streamline their business processes.
A financial services firm implemented robotic process automation (RPA) to automate repetitive and time-consuming tasks, such as data entry and report generation. For organizations exploring automation and process management tools, our BPM Software Selection Guide provides an essential resource for choosing the right platform. By leveraging RPA, they reduced the processing time and the risk of errors associated with manual tasks. This allowed employees to focus on higher-value activities, resulting in increased productivity and improved customer satisfaction.
In conclusion, process improvement is vital for organizations striving for growth and success. By implementing user-friendly processes, reducing waste, utilizing process visualization tools, creating standardized processes for scalability, and streamlining business processes with automation, organizations can achieve significant improvements in their operations. These examples serve as inspiration for organizations seeking to enhance their processes and stay ahead in today’s competitive business environment.
Conclusion
The four exemplary approaches to process improvement that organizations can draw inspiration from in today’s dynamic business landscape. Emphasizing user-friendly processes, as demonstrated by a manufacturing company’s simplification efforts, underscores the importance of clarity and efficiency in task execution. Identifying and eliminating waste, exemplified by a healthcare organization’s lean management adoption, showcases the benefits of streamlining operations for enhanced efficiency. The use of process visualization tools, as illustrated by a logistics company, empowers organizations to gain holistic insights, identify bottlenecks, and foster collaboration. Standardizing processes, as seen in the retail company’s expansion, lays the foundation for scalability, consistency, and customer satisfaction. Lastly, automating business processes, exemplified by a financial services firm’s RPA implementation, underscores the transformative impact of technology on productivity and error reduction. These examples collectively emphasize the significance of continuous process improvement in meeting customer demands and staying competitive in the modern business world.
Frequently Asked Questions
Implementing user-friendly processes in an organization offers several benefits. It enhances productivity by making tasks easier to understand and execute, reducing errors and inefficiencies. Moreover, user-friendly processes improve employee satisfaction as they experience less frustration and stress while working. Clear instructions and visual aids also facilitate faster onboarding for new employees. Ultimately, fostering a work environment that is more efficient and characterized by harmony.
Spotting and cutting waste in your business routines boosts efficiency and reduces costs. A detailed analysis will reveal repeated tasks or resource overuse. Removing these streamlines operations, quickens cycle times, and increases productivity. This results in cost savings, happier customers, and a stronger market position.
Improving your business efficiency with automation involves few simple steps. Firstly, pinpoint the repetitive tasks like data entry or document handling – these are ripe for automation. Next, explore suitable automation tools like RPA or workflow software. Then, develop and integrate automated workflows with your existing systems. Afterwards, train your team on these new processes. Finally, monitor these workflows for performance and make adjustments as required. By doing so, you’ll reduce manual labor, decrease errors, and significantly elevate your organization’s overall efficiency.